

If such a compound is used, then choose low or medium strength. The drawback to these compounds is that they can cause difficulty when the knobs are replaced. Thread-locking compounds are OK, but unnecessary. One way to ensure proper installation is with a torque wrench and a special retention knob socket.ģ. Over-tightening increases the chance of breakage during use, so torque to between 90 and 100 percent of these maximum values. In general, tighten 30- and 35-taper retention knobs to no more than 40 foot-pounds of torque tighten 40-taper knobs to no more than 85 foot-pounds and tighten 50-taper knobs to no more than 110 foot-pounds. Another is that the compound might let the knob vibrate loose during machining. This is one reason not to use a lubricious compound.
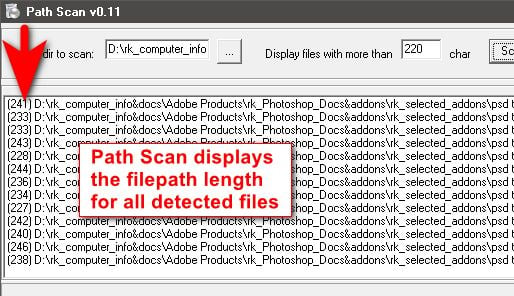
Without this friction, the proper amount of torque may cause the knob to stretch too far. The normal friction between threads and flange surfaces is useful for retention knobs. Clamprite’s Jerome Sailing offers the following tips for correctly applying this critical link between toolholder and spindle.
IS THERE A PROGRAM COMPARABLE TO LONG PATH TOOL INSTALL
Inspect them regularly and install replacements correctly. Toolholder “pull studs,” or retention knobs, are meant to be replaced. Sidebar: Proper Installation Of Retention Knobs The response to fretting thus encourages more fretting. As a result, during heavy cuts, the slightly smaller toolholder is even freer to move, with the gap between holder and spindle taper allowing even more coolant and metal particles to rise into the space through capillary action.

This degrades its accuracy, and the largest diameter often gets deformed the most. Each time they do this, they remove a small amount of material from the taper. They remove it by hand using an abrasive cloth. Some machinists deal with fretting in a counter-productive way. Chatter and other vibrations, as well as bacteria in the coolant, will all contribute to fretting. This coppery discoloration on the toolholder’s taper is caused by microscopic welding of the holder and spindle. Repair the drawbar whenever holding force has dropped below 90 percent of the manufacturer’s specification.įretting is another symptom that the drawbar force may be too low. That’s why any significant drop from the optimal value is likely to be too much. If they did, then the bearings would be overloaded. When to repair the drawbar: Spindles don’t come with a lot of excess holding force, he says.Because HSK spindles require high drawbar force in order for the toolholder to properly engage with the spindle face, these machines merit more frequent drawbar testing. HSK spindles are another matter, requiring nearly twice the force of comparable long-taper spindles, Mr. Some 50-taper machines will require 9,000 pounds of force or more. In general, however, 40-taper spindles will specify 1,800 to 2,500 pounds of force, and most 50-taper spindles will specify 3,800 to 4,800 pounds of force. Only the manufacturer can say for certain what the force should be. Proper force: The optimal drawbar force will also vary, differing even between similar machine models.The life will depend on a number of variables, including the demands of the cutting application and the frequency of tool changes. How long to expect between drawbar repairs: Maybe 2 years or maybe 5.Frequency of inspection: Check drawbar force every 2 months, he recommends.Factor in spindle grinding and lost productivity from downtime, he says, and a machine crash resulting from a tool pulling out of the spindle could cost more than $10,000. Though repairing a drawbar costs hundreds of dollars, the damage that results from neglecting it can cost much more. Jerome Sailing has seen the effect this inattention can produce. However, clamping is also performed by the spindle drawbar-a clamping mechanism that often does not draw enough attention. The various tool clamping choices such as screws, collets, hydraulics and shrink fit all make it easy to focus on the toolholder’s connection to the tool. A toolholder does hold the tool for the machining center, but the toolholder itself is a component that has to be held. The term “toolholder” contains a touch of irony.

This damage to the toolholder is matched by damage inside the spindle taper. Fretting-seen here in the discoloration on the toolholder-is a symptom indicating that the drawbar may no longer be holding the toolholder tightly enough.
